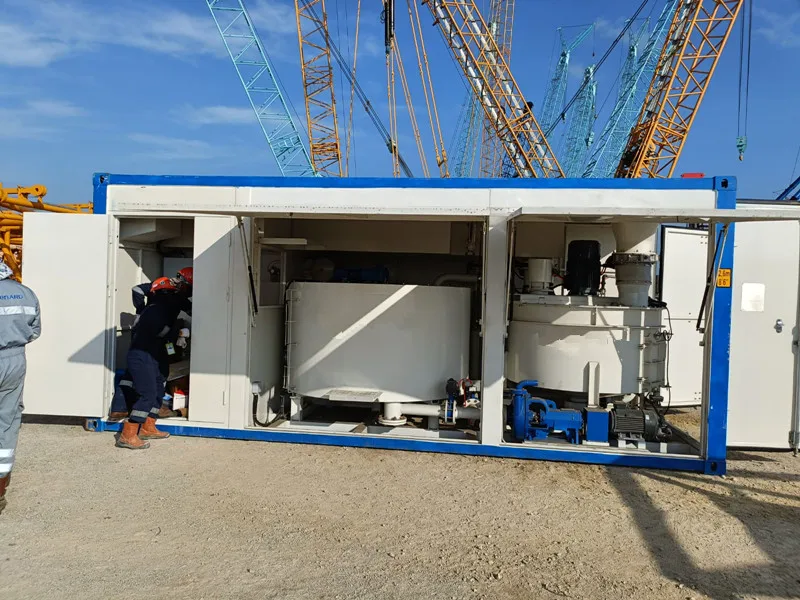
Project introduction
This is a Grout batching plant+Big bag cement silo project for Indonesian customer.The customer needed to transfer sites, and our 20GP container-shaped grout batching plant perfectly met their actual needs.
And their cement is from bags, so we designed the Big bag silo to be used with the Grout batching plant. It realizes the automation of the entire process from cement bag breaking, transportation to grout plant mixer, and finally production of finished mud. It greatly improves customer work efficiency and saves time and costs.
What is the 20GP container-shaped grout batching plant?
Grout batching plant is usually used in tunnel construction, foundation construction and other projects.Usually cement, water, additives, and bentonite are used as raw materials for mixing, and finally transported to the required place through a configured mud pump.
SDDOM considered transportation, installation and customer construction site transfer issues, and made the equipment into the shape of a 20GP container. Allowing customers to avoid foundation construction and difficulty in installation.
Depending on the customer's raw material storage methods, the grout batching plant can be used with different types of silos,like vertical bolted silo,horizontal silo and big bag silo.
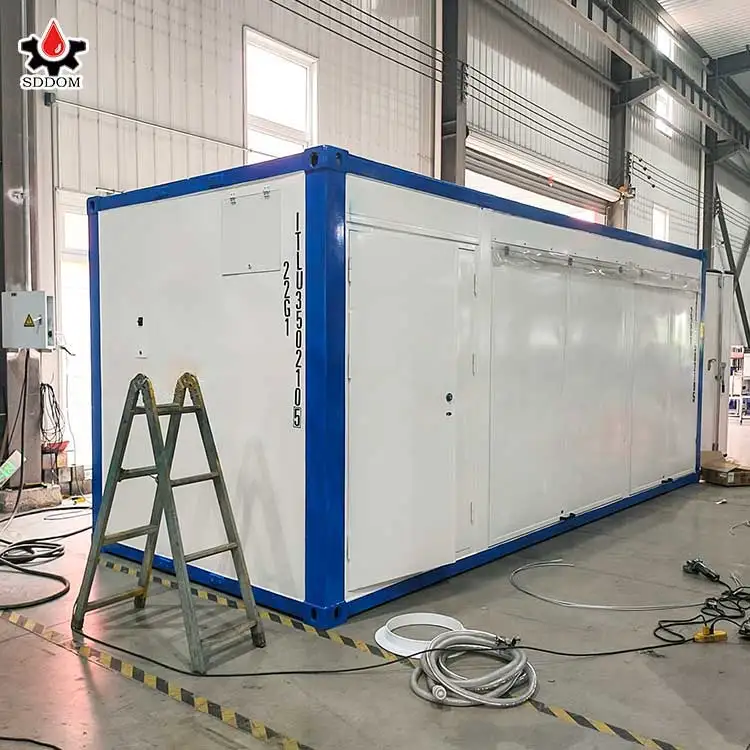
Why customer choose our products?
1,Quality assurance
Shandong DOM Machinery Equipment Co., Ltd. is established in 2014, products have been exported to more than 20 countries in Southeast Asia, Middle EastAfrica. South America. Latin America and so on.Our companyalways adheres to the spirit of "quality first, customers firsthonesty and trustworthiness, and aggressiveness". CE and ISO9001 certification are avaliable.
The raw materials, steel, and accessories used in the products are all from large manufacturers, and the quality is guaranteed from the source.
The thickness of the entire steel used in the grout plant is over 4mm and can withstand 3 layers of stacking.
2,Amazing design.
SDDOM have excellent designers, experienced technicians anostrict supervisors.From design, research and development to production and installation, there are dedicated personnel in charge. Really provide customers with one-stop purchasing.
We made the shape of the grout plant into a standard container style, fully considering customer installation and transportation issues. Save customers’ follow-up costs.
According to the customer's special incoming material method, matching raw material conveying equipment is designed, and all projects can be customized.
Design products that fully meet customer needs.
3,Good service
Whether it is preliminary design communication, delivery matters, or even installation and commissioning guidance at the project site, we have professional and dedicated personnel to take charge. We will also regularly conduct follow-up visits to customers and provide remote online guidance. And according to customer needs, spare parts for wearing parts are provided. Truly allow customers to feel assured, worry-free and at ease.
The project received high praise from the customer and long-term cooperation.